The production of alfalfa pellets plays a crucial role in the agricultural and livestock industries by providing a reliable, nutrient-rich feed source for animals. However, like any industrial process, pellet production also carries a potential environmental impact, particularly in terms of energy consumption, waste generation, and carbon emissions. As demand for sustainable and eco-friendly practices grows, addressing the environmental footprint of alfalfa pellet production is becoming increasingly important.
This article will examine the environmental impact of alfalfa pellet making machines, explore sustainable practices to mitigate negative effects, and highlight innovations that are helping the industry move toward greener solutions.
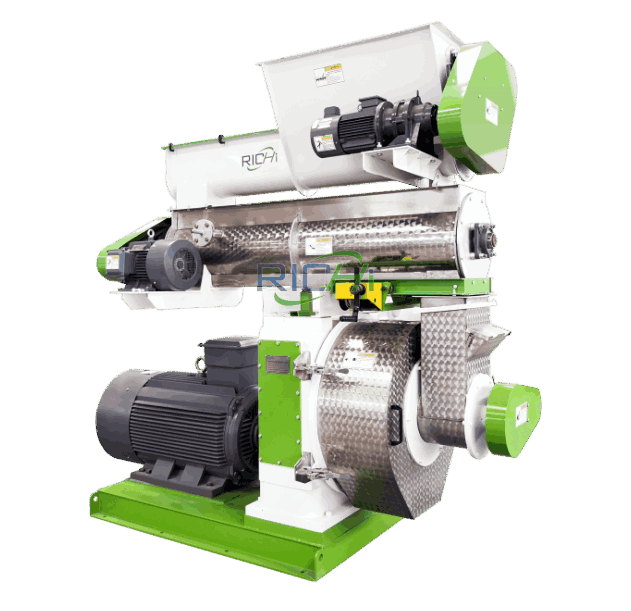
1. The Environmental Impact of Alfalfa Pellet Production
A. Energy Consumption and Carbon Emissions
Pellet production, especially for large-scale operations, requires substantial energy input. The process of converting raw alfalfa into pellets involves drying, grinding, conditioning, and pressing, all of which consume energy. The energy demand is typically met by fossil fuels, which contribute to carbon emissions. This can be a significant environmental concern for pelletizing operations that rely on non-renewable energy sources.
i. Electricity Usage
The use of electricity in pellet production accounts for a significant portion of energy consumption. The production of alfalfa pellets often involves machinery such as grinders, pellet mills, and dryers, which can consume large amounts of electricity. These machines are typically powered by electric motors, and in many cases, the electricity comes from grid systems that rely on fossil fuels, further contributing to environmental pollution.
ii. Fuel Consumption for Drying
Drying alfalfa to the correct moisture content before pelletizing requires substantial heat, often produced by natural gas or coal. This contributes to both air pollution and carbon emissions. The energy consumption during this phase is particularly high, as it involves evaporating moisture from the raw material, which is energy-intensive.
2. Sustainable Practices in Alfalfa Pellet Production
To minimize the environmental footprint of alfalfa pellet production, several sustainable practices can be implemented at various stages of the process. These practices help reduce energy consumption, lower carbon emissions, and limit waste generation, making the industry more eco-friendly.
A. Use of Renewable Energy Sources
One of the most significant ways to reduce the environmental impact of pellet production is to switch to renewable energy sources. By using clean energy to power pelletizing machines, manufacturers can drastically reduce their carbon emissions.
i. Solar Power
Utilizing solar energy to power machinery and lighting systems can significantly reduce the reliance on fossil fuels in pellet production. Solar panels can be installed on-site to generate electricity, which can be used to power various machines such as grinders, pellet mills, and dryers. This renewable energy source provides a sustainable solution that reduces carbon emissions and helps the pellet production facility achieve greater energy independence.
ii. Biogas Utilization
Another promising renewable energy source is biogas. Some pellet production facilities have started using biogas as a fuel for drying and heating systems. Biogas is typically produced from organic waste and is a cleaner alternative to natural gas or coal, resulting in fewer greenhouse gas emissions. It is also a sustainable option because it repurposes waste materials that would otherwise contribute to environmental pollution.
B. Energy-Efficient Equipment
To further minimize the environmental impact of pellet production, manufacturers are adopting energy-efficient equipment designed to reduce power consumption. These advancements include:
i. High-Efficiency Motors
Pellet mills and other machines in the production line can be equipped with high-efficiency motors that reduce electricity consumption without compromising performance. These motors use advanced technology to optimize energy use, thereby reducing the amount of power needed to operate the machinery.
ii. Heat Recovery Systems
Many modern pelletizing systems incorporate heat recovery technology to capture waste heat generated during the production process. This recovered heat can be used to pre-heat materials, reducing the need for additional energy inputs. This not only lowers the overall energy consumption of the plant but also contributes to cost savings for the producer.
3. Reducing Waste Generation in Pellet Production
A. Material Recycling and Upcycling
During the pellet production process, some waste is inevitable. However, it is possible to minimize waste generation through effective material recycling. By upcycling raw material waste, manufacturers can reuse byproducts such as wood chips, sawdust, or alfalfa dust in other industries, such as biomass energy production or as animal bedding.
i. Reprocessing Alfalfa Dust
Alfalfa dust, which often accumulates during grinding and pelletizing, can be collected and reprocessed into smaller pellets or used as a filler in other products. This reduces the amount of waste generated and contributes to a more circular economy by finding alternative uses for materials that would otherwise be discarded.
ii. Improved Material Handling
Efficient material handling systems can help reduce waste during the processing phase. Automated systems that provide continuous, consistent feeding of raw material into the pellet mill can reduce material spillage and ensure that all of the alfalfa is utilized efficiently.
4. Pellet Durability and Packaging Innovations
In addition to improving the efficiency of the production process, enhancing the durability of the pellets themselves can have a positive environmental impact. Stronger pellets result in less breakage, reducing waste during transportation and storage.
A. Sustainable Pellet Packaging
Innovations in packaging materials are also contributing to more sustainable pellet production. Traditional plastic packaging, which can contribute to landfill waste, is being replaced with biodegradable and recyclable materials. Using eco-friendly packaging reduces the overall environmental footprint of the product, contributing to a more sustainable lifecycle for the pellets.
B. Durable Pellets with Reduced Breakage
By incorporating natural binding agents and improving the pelletizing process, manufacturers can produce more durable pellets that are less likely to break or degrade during handling. This reduces the amount of dust and broken pellets, which can be recycled back into the system for further processing, minimizing waste and making the entire operation more sustainable.
5. Carbon Offsetting and Sustainability Certifications
A. Carbon Offsetting Initiatives
In addition to reducing emissions at the production level, some companies are also investing in carbon offset programs to balance out the emissions generated by their operations. These programs support projects that reduce greenhouse gases, such as reforestation initiatives or the installation of renewable energy systems.
B. Sustainability Certifications
In an effort to meet growing consumer demand for environmentally friendly products, many pellet manufacturers are seeking sustainability certifications from organizations such as the Forest Stewardship Council (FSC) or ISO 14001. These certifications help ensure that production processes are environmentally responsible and that the business is committed to sustainable practices.
6. The Future of Alfalfa Pellet Production: Green Technologies and Innovations
The future of alfalfa pellet production will be shaped by the continued adoption of green technologies and sustainable practices. As environmental concerns continue to take center stage in the agricultural industry, pellet producers will increasingly turn to innovative solutions to reduce their environmental footprint.
A. Carbon-Neutral Pelletizing Plants
As part of the broader trend toward carbon neutrality, future pelletizing plants are expected to incorporate technologies that allow them to become carbon-neutral. This could involve using renewable energy sources, implementing waste-to-energy technologies, and adopting sustainable production practices to achieve a net-zero carbon footprint.
B. Integration of Artificial Intelligence for Sustainability
AI technologies will continue to play a role in optimizing energy usage and reducing emissions. AI-driven systems can predict and adjust operations to optimize energy consumption, improve machine performance, and reduce waste generation, leading to more sustainable production methods.
7. Conclusion: Striving for Sustainability in Alfalfa Pellet Production
As the demand for sustainable and eco-friendly practices increases, the alfalfa pellet production industry is evolving to meet these challenges. By integrating renewable energy sources, improving energy efficiency, reducing waste, and adopting green technologies, pellet manufacturers are taking significant steps toward reducing their environmental impact. (Related post: Grass Pellet Machine)
The transition toward more sustainable practices in alfalfa pellet production will not only benefit the environment but will also support the long-term viability and growth of the industry. The future of alfalfa pellet production lies in greener solutions, ensuring that feed production can meet the needs of livestock while minimizing the environmental footprint.