A 10 tons per hour (t/h) fish feed production facility is a significant industrial venture that demands considerable energy input, primarily in the form of electricity. The electricity consumption of such a facility can vary widely across different countries due to various factors, including climate, energy efficiency standards, equipment quality, and local energy policies. This article examines how electricity consumption for a 10t/h fish feed mill engineering differs across regions and the key factors that influence these variations.
Key Factors Influencing Electricity Consumption
- Climate and Temperature
Countries with extreme climates may require more energy for climate control within the plant. Hot climates necessitate increased cooling, while cold climates may require additional heating. - Energy Efficiency Standards
Countries with stringent energy efficiency regulations often exhibit lower overall electricity consumption due to the use of more efficient machinery and processes. - Equipment Quality and Age
Newer, high-quality equipment tends to be more energy-efficient compared to older or lower-quality machinery. - Production Process Efficiency
The overall design and efficiency of the production process can significantly impact electricity consumption. - Raw Material Characteristics
The type and quality of raw materials used can affect the energy required for processing, particularly during grinding and extrusion stages. - Operational Practices
Plant management practices, including maintenance schedules and operator training, can influence energy efficiency. - Electricity Grid Reliability
In countries with unreliable power grids, the reliance on backup generators or the need for frequent equipment restarts can increase overall energy consumption.
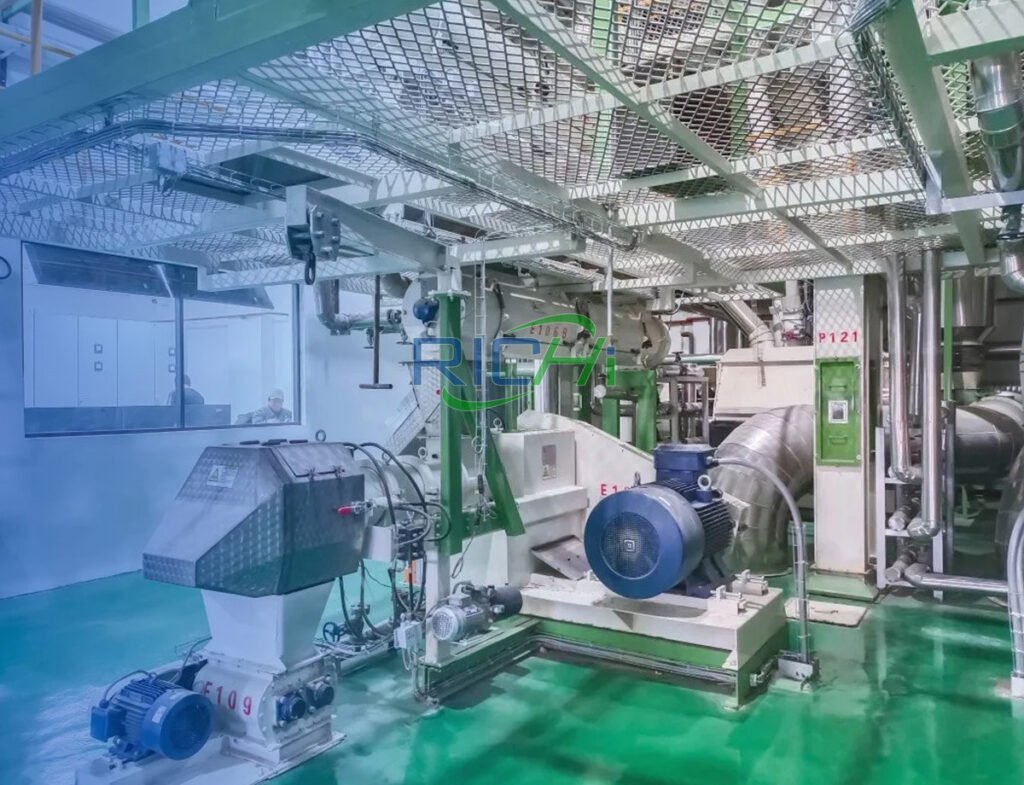
Electricity Consumption in Various Countries
- China
Estimated Consumption: 450-500 kWh per ton of feed produced
Key Factors:- Relatively low energy efficiency standards in some regions
- Varied equipment quality across different manufacturers
- Government initiatives promoting energy efficiency in industrial sectors
Example: A 10t/h plant in China might consume around 4,500-5,000 kWh per hour of operation.
- United States
Estimated Consumption: 380-420 kWh per ton of feed produced
Key Factors:- High energy efficiency standards
- Advanced technology and automation
- Strict environmental regulations promoting energy-efficient practices
Example: A 10t/h plant in the US might consume approximately 3,800-4,200 kWh per hour of operation.
- Norway
Estimated Consumption: 350-390 kWh per ton of feed produced
Key Factors:- Very high energy efficiency standards
- Cold climate requiring additional heating
- Advanced technology in the aquaculture sector
Example: A 10t/h plant in Norway might consume around 3,500-3,900 kWh per hour of operation.
- Vietnam
Estimated Consumption: 480-530 kWh per ton of feed produced
Key Factors:- Tropical climate requiring significant cooling
- Varying equipment quality and efficiency
- Rapidly growing aquaculture sector with improving standards
Example: A 10t/h plant in Vietnam might consume approximately 4,800-5,300 kWh per hour of operation.
- Brazil
Estimated Consumption: 420-470 kWh per ton of feed produced
Key Factors:- Diverse climate conditions across the country
- Improving energy efficiency standards
- Mix of new and older equipment in the industry
Example: A 10t/h plant in Brazil might consume around 4,200-4,700 kWh per hour of operation.
- India
Estimated Consumption: 500-550 kWh per ton of feed produced
Key Factors:- Hot climate requiring significant cooling
- Varying equipment quality and efficiency
- Improving but still developing energy efficiency standards
Example: A 10t/h plant in India might consume approximately 5,000-5,500 kWh per hour of operation.
- Germany
Estimated Consumption: 360-400 kWh per ton of feed produced
Key Factors:- Very high energy efficiency standards
- Advanced technology and automation
- Strong focus on sustainable industrial practices
Example: A 10t/h FISH feed pellet production line in Germany might consume around 3,600-4,000 kWh per hour of operation.
Detailed Breakdown of Electricity Consumption
To better understand electricity consumption patterns, let’s break down the major components of a 10t/h fish feed plant:
- Grinding Equipment (20-25% of total consumption)
Highly dependent on raw material characteristics and generally more efficient in countries with advanced milling technology. - Mixing and Conditioning (10-15% of total consumption)
Relatively consistent across countries, with slight variations due to ambient temperature differences. - Extrusion Process (30-35% of total consumption)
The most energy-intensive part of the process, with efficiency varying significantly based on equipment quality and operational practices. - Drying and Cooling (15-20% of total consumption)
Highly influenced by ambient climate conditions and more energy-intensive in humid tropical climates. - Packaging and Material Handling (5-10% of total consumption)
Generally consistent across countries, with slight variations based on the level of automation. - Auxiliary Systems (5-10% of total consumption)
This includes lighting, HVAC, and compressed air systems, which vary based on local climate and energy efficiency standards.
Strategies to Reduce Electricity Consumption
- Implement Energy Management Systems
Installing advanced monitoring and control systems can optimize energy use throughout the plant. - Upgrade to Energy-Efficient Equipment
Replacing outdated machinery with modern, energy-efficient alternatives can significantly reduce electricity consumption. - Optimize Production Scheduling
Running the plant at optimal capacity and minimizing idle time can enhance overall energy efficiency. - Improve Insulation and HVAC Systems
Particularly important in extreme climates to reduce the energy needed for heating or cooling. - Utilize Renewable Energy Sources
Implementing solar panels or other renewable energy sources can offset grid electricity consumption. - Regular Maintenance and Calibration
Ensuring all equipment is well-maintained and properly calibrated can prevent energy waste due to inefficiencies. - Employee Training and Awareness
Educating employees about energy-saving practices can lead to significant reductions in electricity consumption.
Conclusion
The electricity consumption of a 10t/h fish feed mill factory facility varies significantly across countries, ranging from approximately 350 kWh per ton in highly efficient operations in countries like Norway to over 500 kWh per ton in less efficient plants in countries with challenging climates, such as India. These variations are primarily driven by differences in climate conditions, energy efficiency standards, equipment quality, and operational practices.
Plant operators and investors must carefully consider these factors when planning and operating fish feed manufacturing facilities. While countries with lower electricity consumption may offer cost advantages, it’s essential to also consider factors such as raw material availability, market demand, and regulatory environment.
By implementing energy-efficient technologies, optimizing production processes, and adopting best practices in energy management, fish feed manufacturers can reduce their electricity consumption and operational costs, regardless of their location. As the aquaculture industry continues to grow and energy costs rise, focusing on energy efficiency will become increasingly important for maintaining competitiveness in the global fish feed market.