Investing in a 20 tons per hour (t/h) fish feed pellet production line is a significant commitment within the aquaculture sector. Understanding the primary cost components associated with this setup is essential for effective budgeting, financial planning, and evaluating the project’s overall viability. This article delves into the major cost factors involved in establishing and operating a 20t/h fish feed pellet production line.
Equipment Costs
The machinery and equipment required represent a substantial portion of the initial investment:
- Raw Material Handling Equipment:
- Silos and storage bins
- Conveying systems (screw conveyors, bucket elevators)
- Weighing and batching systems
- Grinding Equipment:
- Hammer mills or pulverizers
- Mixing Equipment:
- Horizontal or vertical mixers
- Conditioning and Extrusion Equipment:
- Steam conditioners
- Single or twin-screw extruders
- Drying and Cooling Equipment:
- Horizontal or vertical dryers
- Counterflow coolers
- Coating Equipment:
- Vacuum coaters for oil addition
- Packaging Equipment:
- Bagging machines
- Palletizers
Estimated Cost Range: $1,500,000 – $2,500,000
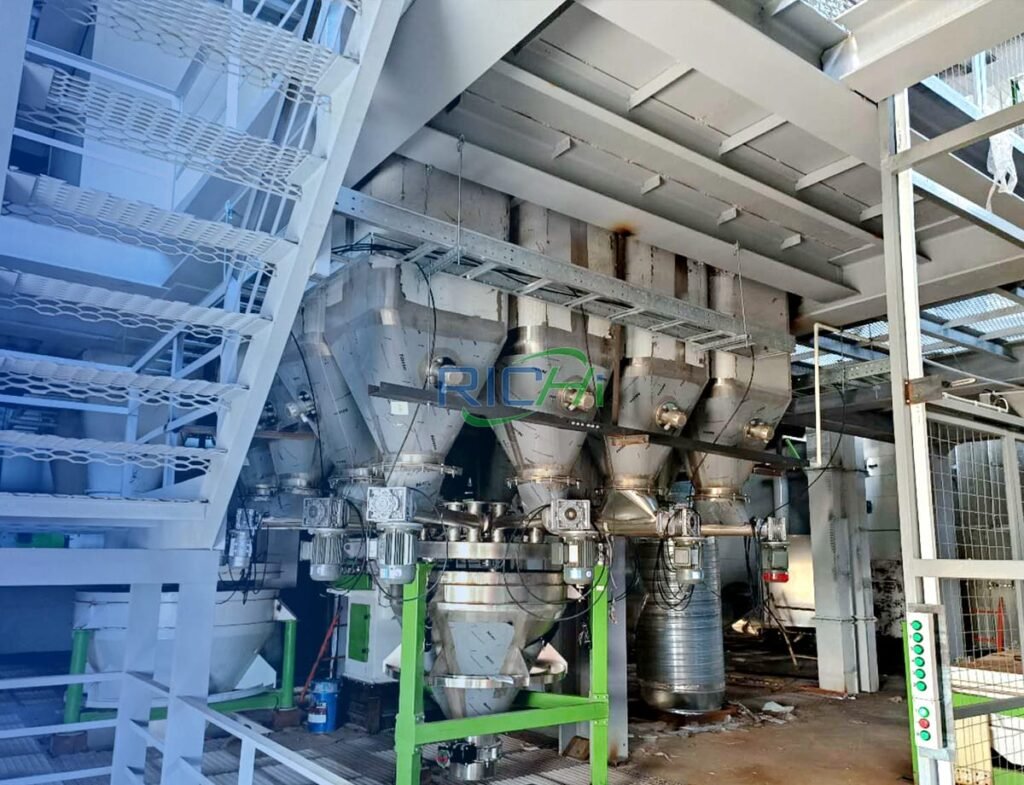
Building and Infrastructure
Establishing a suitable facility for the pellet production line involves:
- Constructing or renovating a factory building
- Laying foundations for heavy machinery
- Installing electrical systems and wiring
- Setting up plumbing and water supply systems
- Creating ventilation and dust collection systems
- Designing office spaces and quality control laboratories
Estimated Cost Range: $500,000 – $1,000,000
Utility Setup and Operational Costs
Ongoing utility expenses contribute significantly to operational costs:
- Electricity:
- Power for machinery, lighting, and climate control
- Water:
- Required for conditioning and cleaning processes
- Steam Generation:
- Boilers for producing steam used in conditioning
- Compressed Air Systems:
- Necessary for pneumatic controls and cleaning
Estimated Annual Cost: $200,000 – $400,000
Raw Material Costs
Raw materials represent the largest ongoing expense in fish feed production:
- Fish meal and fish oil
- Plant-based proteins (soybean meal, wheat gluten)
- Grains and starches
- Vitamins and minerals
- Binders and additives
Estimated Annual Cost (at full capacity): $30,000,000 – $40,000,000
Labor Costs
A skilled workforce is essential for various roles:
- Production operators
- Maintenance technicians
- Quality control personnel
- Supervisors and management staff
- Administrative staff
Estimated Annual Cost: $500,000 – $800,000
Maintenance and Spare Parts
Regular maintenance is vital for optimal operation:
- Routine maintenance supplies
- Replacement parts for wear items (dies, rollers, screens)
- Emergency repair services
Estimated Annual Cost: $150,000 – $250,000
Quality Control and Testing
Ensuring product quality is paramount:
- Laboratory equipment
- Testing supplies
- Third-party analysis services
Estimated Annual Cost: $100,000 – $200,000
Environmental Compliance and Waste Management
Meeting regulatory standards is necessary:
- Dust collection and air filtration systems
- Wastewater treatment facilities
- Solid waste disposal
- Environmental permits and certifications
Estimated Initial Cost: $200,000 – $400,000
Estimated Annual Operational Cost: $50,000 – $100,000
Research and Development
Ongoing product improvement and innovation require investment:
- Formulation development
- Process optimization studies
- New product trials
Estimated Annual Cost: $100,000 – $300,000
Marketing and Sales
Promoting products and maintaining customer relationships involves:
- Marketing materials and campaigns
- Participation in trade shows
- Sales team expenses
- Customer support services
Estimated Annual Cost: $200,000 – $400,000
Insurance and Regulatory Compliance
Protecting the business and fulfilling legal obligations entails:
- Property and liability insurance
- Product liability insurance
- Costs associated with regulatory compliance (FDA, USDA, etc.)
Estimated Annual Cost: $100,000 – $200,000
Logistics and Transportation
Moving raw materials and finished products includes:
- Inbound logistics for raw materials
- Outbound logistics for finished feed
- Fleet maintenance (if applicable)
- Third-party logistics services
Estimated Annual Cost: $500,000 – $1,000,000
Technology and Software
Managing operations and data effectively requires:
- Enterprise Resource Planning (ERP) system
- Manufacturing Execution System (MES)
- Quality Management System (QMS)
- Maintenance management software
Estimated Initial Cost: $100,000 – $300,000
Estimated Annual Operational Cost: $20,000 – $50,000
Training and Development
Ensuring staff competency and compliance involves:
- Initial training for new equipment and processes
- Ongoing skill development programs
- Safety training
- Compliance training
Estimated Annual Cost: $50,000 – $100,000
Financing Costs
If financing the project through loans, consider:
- Interest payments
- Loan origination fees
- Costs varying based on loan terms and amount borrowed
Conclusion
The total initial investment for a 20t/h fish feed pellet production line ranges from $3 million to $5 million, with annual operational costs (excluding raw materials) estimated between $2 million and $4 million. Raw material costs, which can exceed $30 million annually at full capacity, represent the largest ongoing expense.
Conducting a thorough market analysis is essential to ensure sufficient demand for the production capacity. Additionally, careful consideration of the location is vital, as it influences labor, utility, and logistics costs.
Effectively managing these cost components is crucial for the profitability and success of a fish feed pellet production line. Implementing cost-saving measures, optimizing processes, and maintaining high product quality can help secure the long-term viability of the operation in the competitive aquaculture feed market.